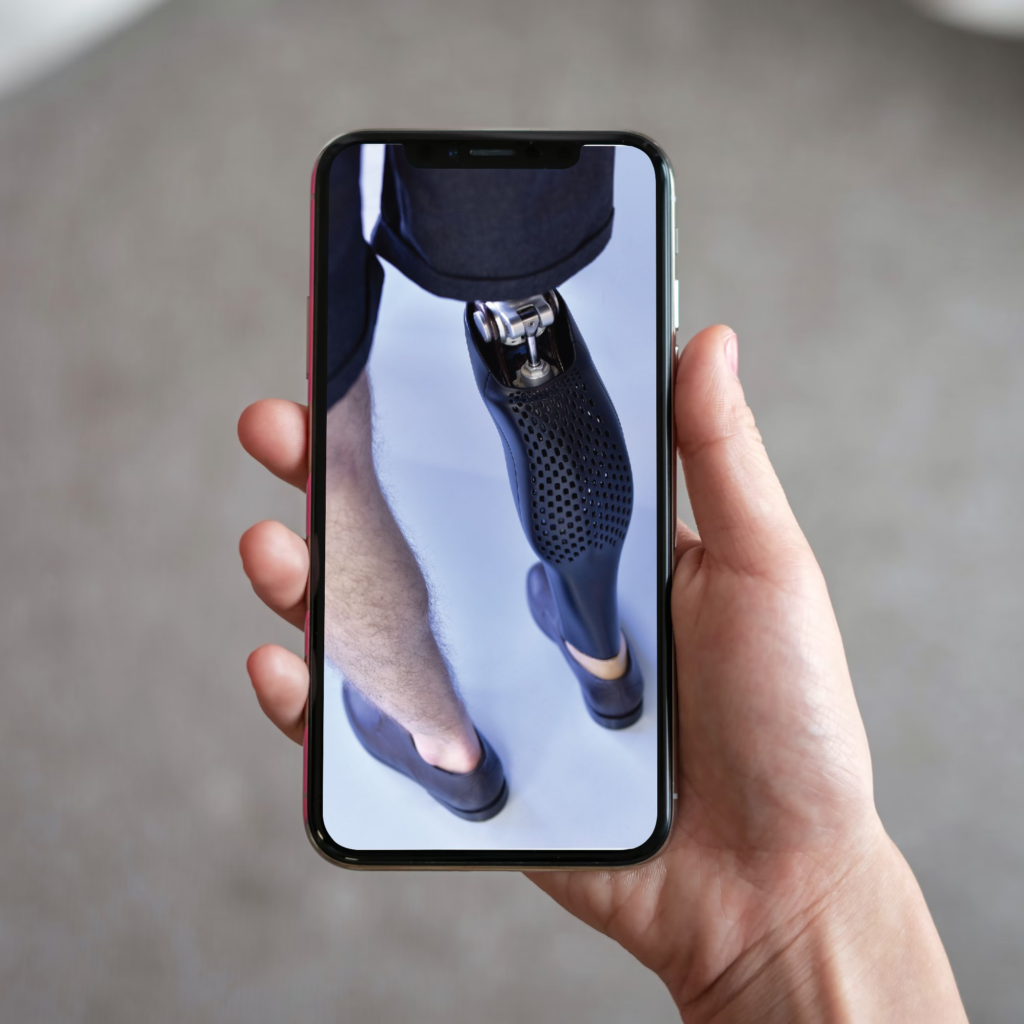
Introduction: What is 3D Technology?
3D printing has come a long way since it was first introduced in the late ’90s. It has become an essential tool for engineers and designers, who can use it to create real objects from digital information.
3D printing is a method of making three-dimensional objects by adding layers of material to build up something that wasn’t there before. In addition to being used for prototyping or rapid manufacturing, 3D printers are also used in industries including automotive, aerospace, construction, and health care industries. These applications have increased in popularity thanks to the precision and accuracy of today’s printers as well as the variety of materials available for 3D printing.
3D Technology in the P&O Industry and How it Works?
3D printing is a technology that has been revolutionizing the world around us, and it’s no surprise that it’s making its way into the medical field. 3D printing is already used to create prostheses for amputees, but now it’s being used in other ways.
3D printing is popular because it allows for customization—and that’s exactly what patients need when dealing with their health problems. The technology can be used to provide them with custom-made parts for prosthetics, which means that a Prosthetist can tailor things to each individual patient’s needs.
There is a 3D printed finger to a complete arm, and in recent years there is a rise in 3D technology within India. The most commonly seen are 3D printed sockets. According to some experts, there has been no shortage of miracles and that continues to happen in the health care system.
How It’s Impacting the P&O Industry
keywords:
why do we need the 3D technology in P&O to understand this we have to break down the fundamental or the key aspect of 3D technology Let’s start with CUSTOMIZATION: When it comes to customizing prosthetic and orthotic devices, 3D printing is the perfect solution.
Since healthcare is a highly individualized service, 3D printing is a perfect solution for this industry. As opposed to fabricating large numbers of identical parts, 3D printing empowers the creation of prosthetic and orthotic devices custom fitted to a patient’s particular anatomy. Thereby enhancing their adequacy.
This process takes less time than it would if each patient were receiving multiple devices made from pre-fabricated components—and thanks to the flexibility afforded by 3D printing technology.
REDUCE THE LEAD TIME: I want to discuss the idea of reducing the lead time in 3D printing. I know there are many people who do not understand what I mean by that, so I want to clarify it.
The lead time for a new device to be produced and delivered is the amount of time it takes to start the process. It can be measured in days, weeks, or even months.
The process we take to make a new device for an individual will take about 3 days approx with all the equipment and experiences with 3D printing provided by the clinician and the tools to manipulate the design within the software which leads to reducing the production time by half.
COST: When you’re dealing with a patient’s health, there’s no room for error. Whether it’s a medical device or part of the treatment plan or just a simple tool in the doctor’s bag, you need to be able to rely on it working exactly as intended and helping your patients get better faster.
But when you’re working with complex objects or parts and devices that need to be custom-made, manually creating them can be incredibly time-consuming and expensive. Luckily, 3D printing has been making waves in the healthcare industry for some time now—and with good reason!
3D printing has enabled doctors to make several iterations before it is printed, helping them to identify any potential errors, and ensuring that the final product is perfect. In addition to the capacity to make custom, complex parts, 3D printing in healthcare is most appropriate for low-volume production meaning costs will drop while effectiveness increases. Costly tooling or machining processes are no longer needed. Also, waste is reduced which further reduces the costs.
COMPLEXITY: The ability of 3D printers to create organic shapes is what makes them so revolutionary. Before conventional manufacturing may have struggled to create complex, organic shapes, but the designs that 3D printers are now able to produce are potentially limitless.
The ability of these machines to create complex designs with organic shapes is what makes them so revolutionary.
3D printing has come a long way. These machines are able to produce designs that can be scaled up or down, allowing for more variety in the design and production process.
The conclusion
With the advancement of 3D printing, prosthetics are starting to look more like real human limbs.
It’s an exciting time for prosthetic technology, and it may be a great opportunity for P&O. With this in mind, where do I stand on the future of P&O? When talking specifically about prostheses, these are such personal items—each one has to be custom-made or fit to the needs of the wearer. 3D printing changed all this and is now regularly being used to produce patient-specific components of prosthetics that match perfectly with the user’s anatomy. I think 3D technology has lots of potential in it but it’s still in an early stage of development; if adapted with open arms and used cautiously, it can be a pillar for the future P&O field if adapted with open arms and used cautiously.